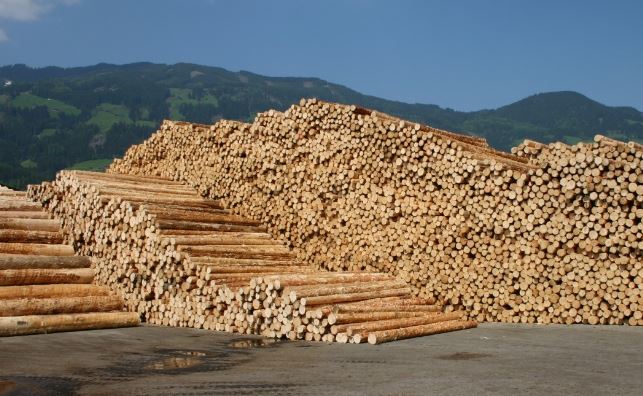
As March began, softwood traders continued to face an uncertain
market with demand only showing signs of a marginal increase
over the previous 2 months, still lagging behind most peoples’
expectations. The forward market showed a modest improvement,
but as always, it was product-specific rather than across all
softwood groups, and the main ongoing casualty was still C24.
As the staple product in importers’ and merchants’ yards for
many years, graded carcassing has taken up large areas of
stocking space. With the number of sizes and lengths needed to
service the market, carcassing has tied up a high level of
financial investment and cash, yet it remains stuck as a low
profit product. Suffering from perhaps the most erratic section
of the market, it has brought some businesses to their knees due
to stock write downs through a perpetual series of extreme peaks
and troughs in both demand and price.
In the current climate, credit insurers are adopting a very
cautious approach to the limits granted in the timber
merchanting sector. During the past year, a number of
well-established merchants have either lost money (and still are
losing money) or have failed altogether, and this has affected
confidence to the point where insured limits have been withdrawn
altogether.
As March progresses, raw material shortages and increased log
costs are starting to bite, and regardless of demand, prices are
rising and recovering from the very low levels that prevailed in
Q4 of last year. Regular increments are now being heralded by
producers that will come into play on a monthly basis.
Last autumn, Baltic processors found the market unworkable, as
increases in log costs far outweighed the levels of return they
could expect from UK buyers. As mentioned in previous reports,
many of the producers switched away from building specifications
in favour of wood fuel, pallet wood and agricultural fencing.
Even today at many ports, it is still evident that the trade in
Latvian C24 and batten material has been substituted by rounded
posts and general landscaping products.
Now a similar situation has arisen in Sweden in terms of raw
material costs and supply. To balance supply and demand, mills
in the south have suspended production for varying periods
rather than just reducing shifts as they have done in the past.
These decisions have been made by the Swedes to avoid
loss-making, and by their efforts to control output, they have
help trigger increased prices along the supply chain.
March is the first month to witness any meaningful price
increases since last summer, but once again, merchants express
concerns that prices could go into reverse gear, so it is vital
for the industry that shippers try to ensure a level of
stability is maintained.
The volume of UK softwood imports for last year rose by
approximately 86,000m3 (+1.5%)* according to Timber Development
UK (TDUK) and the sterling value moved in parallel, indicating
that the average price index was unchanged from 2023. Within the
figures it was noted that Sweden’s exports to the UK had eased
downwards while Latvia made a gain.
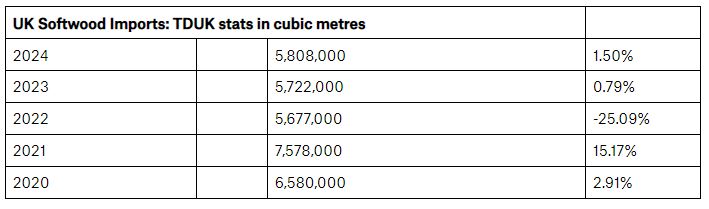
At the year-end, Sweden remained in first position with 47%
of the UK market (2,729,000m3), Latvia second with 17%, followed
by Finland at 12%, with Germany and the Irish Republic at 8%
each.
A brief snapshot of the joinery and quality grades, shows that
there has been a gradual reduction in the average diameter of
harvested Nordic/Scandinavian redwood logs. This has resulted in
a higher portion of centre-cut material reducing the volume of
sideboards in both unsorted and fifth grades.
With shortages of whitewood logs in some areas of Sweden,
volumes of kiln dried redwood have been switched towards treated
carcassing. Redwood enables merchants and importers to achieve
both UC3 & 4 treatment performance levels, something which they
are unable to do with spruce due to its lower porosity which
inhibits the penetration of preservatives.
Looking to the future, off-site timber frame construction,
cassette floors and engineered wood structural beams are all
growing in demand, while solid wood joist designs are being
specified less, particularly for new housing developments.
The housing market is a hot topic, not just in the timber trade,
but also across the national media where a consensus among
housebuilders highlights the fact that the current push for
planning reform seems to be only focused on the major developer.
Apparently, there are around 2,500 registered small to
medium-sized builders capable of erecting sites of between 10-20
houses, and they are reporting that they are struggling more
than ever to get planning approval. These developers are more
likely to use solid wood joists as opposed to multiple house
sets designed in I-joists and LVL and are therefore an important
outlet for solid softwood joist consumption.
To meet the government’s target of 1.5 million new homes during
their term in office, the collective voice of the housebuilding
industry is warning that all sizes of building companies must
receive active assistance to overcome red tape, and they all
need to be involved if the initiative is to stand a chance of
succeeding.
Source: ttjonline.com