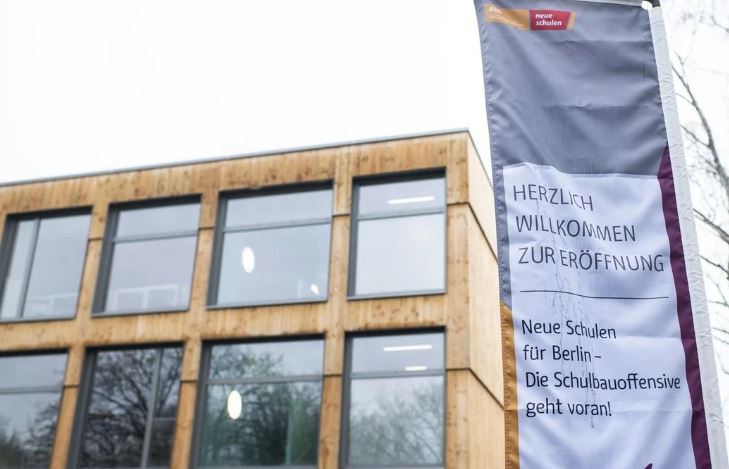
The Sewanstrasse Primary School in
Lichtenberg, Berlin, was built in just eight months. The secret?
Modular timber construction
Berlin. The Senate Department for Urban Development takes a
positive view. But the leap to mass production is still to come.
According to calculations by the Senate Department for Urban
Development, Berlin will need to build 20,000 flats a year in
the coming years. In addition, schools, daycare centres and
sports halls must also be built in the new residential
districts. In order to make Berlin's urban development
sustainable and ecological, the Senate intends to increasingly
use wood to replace climate-damaging concrete. While the project
produced very few results in previous years, the wood strategy
has recently shown clear successes.
In the years from 2021 to 2024, a total of 46 new schools and
school extensions as well as sports halls were built in Berlin
by the public sector, mostly in timber hybrid construction. In
addition, there were nine daycare centres, two research and two
administration buildings, as well as three new buildings for the
volunteer fire brigade.
Timber hybrids conquer the housing market
The state-owned housing associations (LWU) are also increasingly
building with wood: a total of 14 projects have been completed
in timber hybrid construction. Most of the projects involved not
just individual apartment blocks, but entire ensembles with more
than a hundred flats each.
In the past three years alone, a total of 76 building complexes
have been constructed using this renewable building material,
according to the Senate Department for Urban Development's
response to a question from Berlin Green Party MP Andreas Otto.
For comparison: The timber construction atlas of the ‘Natural
Building Lab’ of the Technical University (TU) Berlin listed
exactly 51 projects in Berlin by 2021, which, depending on the
type of construction, were built in the categories of timber
module, timber frame, solid timber, timber façade or timber
frame construction.
From a ridiculed eco-project to a real economic factor
‘When timber construction appeared in the red-red-green
coalition agreement in 2016, many people laughed,’ recalls
Andres Otto. In the meantime, however, building with wood has
survived the trial period. ‘The renewable building material has
arrived in Berlin and become a real economic factor,’ says Otto.
And emphasises that since its beginnings in 2016, numerous
cooperatives and private investors have realised a number of
model projects alongside the public sector. ‘Now the timber
house still has to go from being a model project to a mass
product,‘ hopes the Greens’ construction policy spokesperson.
Timber construction is also becoming increasingly competitive
with Conventional construction through the industrial
prefabrication of elements and modules. Three large companies in
the region - B&O, Nokera and Timpla - have already built up
industrial capacities and could provide significant support for
residential construction in Berlin. ‘Wood grows in abundance,
especially in Brandenburg. To keep it that way, the forest must
be ecologically reorganised,’ demands the Green politician.
Building with wood is a small but not insignificant step towards
achieving Berlin's climate targets, emphasises Otto. Every cubic
metre of wood contains almost a tonne of CO₂. Every wooden house
is a CO₂ store, perhaps for centuries. In contrast, steel and
cement blow plenty of greenhouse gas into the air during
production.
Source:
morgenpost.de