¡¡
US housing starts decline to lowest level since 1993
Housing starts in the US during the month of September were down 10.2% from August and
30.8% less than in September 2006, reported Random Lengths International. This is the lowest housing starts have fallen since 1993,
the time when the last housing crisis occurred in the US. With housing starts on the decline, some experts have
expressed worry that the US economy could suffer a blow in the near future. Improvements in the housing situation
seem unlikely in the near future, as housing starts fell 7.3% in September, and recent polls have revealed low
home builder confidence. It is hoped that the latest Federal Reserve¡¯s move to lower interest rates will
help stave off the housing crisis¡¯s impact on the US economy.
Canada¡¯s primary and secondary wood industries brace for challenging times ahead
Prior to 2006, North American producers of engineered wooden boards experienced a three-year period of
profitable business conditions and most producers of Oriented Strand Board
(OSB) undertook major capital investments. These include:
Louisiana-Pacific/Canfor¡¯s Peace Valley mill in British Columbia, Canada, with 800
million ft2, bringing LP¡¯s share of the North American
OSB market to 23%; Grant Forest Products Inc.¡¯s mills in South Carolina, with 800 million ft2;
Langboard¡¯s new line at Quitman, Georgia, with 440 million ft2; Norbord Inc.¡¯s
Cordela, Georgia, expansion of 550 million ft2 bringing the company¡¯s total capacity close to one billion
ft2; Martco¡¯s OSB mill in Oakdale, Louisiana; and Ainsworth¡¯s new mill in Alberta, Canada, capable
of producing OSB and/or OSL.
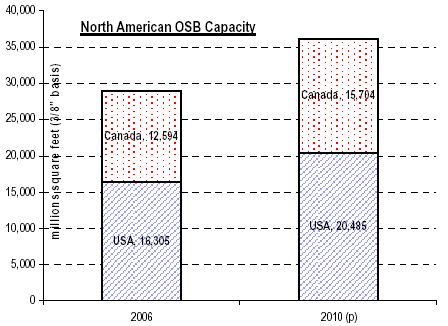
In addition, more previously planned OSB expansion projects are coming on line within the next few years,
adding over seven billion ft2 of capacity by the end of 2010. Prominent future
investments include: Louisiana-Pacific¡¯s new mill in Clarke County, Alabama, which is
scheduled to start in early 2008; Arizona Forest Restoration Products Inc. (AFRP), which is
planning a Greenfield OSB mill near Flagstaff, Arizona in 2009, and would reach a capacity of
680 million ft2; and Ainsworth Lumber Co. Ltd., which intends to open new OSB mills in
the interior of British Columbia and Manitoba, Canada. Additionally, Huber Engineered Woods plans a new 650
million ft2 OSB mill in Georgia but the starting date is not yet determined. Grant
Forest Products Inc. is working on plans for a second mill in Clarendon County and Kruger
Inc. plans to build a 750 ft2 per year OSB mill in Northern Ontario, Canada, to be ready at the end of 2008, although
the implementation of these plans have been slowed.
The good fortunes in the structural panel industry have now changed dramatically. In 2005, US housing starts
stood at a peak of 2.07 million units but in mid-2006, the market started to
nose-dive. Poor affordability, rising interest rates and diminishing consumer confidence began
to take their toll. Last year, 1.81 million new housing units were registered, but the number this
year is likely to only reach 1.4 million. The situation is not likely to improve
before the end of 2008, considering that there is currently a nine month inventory of unsold houses in the USA.
Experts predict for next year a dismal number of 1.2 million new units.
The decline in the US housing market is causing a major supply/demand imbalance. With panel production
booming in Asia and Europe, there will be no relief from offshore export markets, this despite of low OSB prices
and the declining value of the dollar. It is expected that structural wood panel consumption (plywood and
OSB) will be lower by up to 6 billion ft2 in 2007 from its peak level in 2005. In April of 2004 - when prices reached its
culmination - OSB stood at US$ 520 per 1000 ft2 ¨C almost four times the current level.
In addition to the declining demand and sagging prices, panel mills are plagued by high fiber and energy costs.
Plywood mills are particularly burdened given their obligation to comply with
expensive new Maximum Achievable Control Technology (MACT) regulations. Not
all regions in the US are equally affected by the slump. There is a relative scarcity of mills in the US
southwest (e.g. Arizona), and such major cities as Los Angeles, Phoenix and Las Vegas
continue to create a satisfactory demand for wooden panels.
In view of the dismal American housing market, panel producers are scaling down and delaying their growth
plans or canceling new mill constructions altogether. Some mills will close or merge with other players. For
instance, Louisiana Pacific (LP) closed its St Michel, Quebec, facility late last year but there is a slight chance
that it will re-open again at a later time. Another OSB mill planned by LP has been put on hold, possibly until 2009.
Ainsworth indefinitely closed two of three OSB mills in Minnesota in September 2006. The company permanently
closed a 280 ft2 line in the third plant. Ced-Or Corp. also announced it will not build the cedar OSB mill planned
since 2000 and has been facing serious financial problems.
It seems that value-added products are suffering less under the current economic downturn.
Many of the new mills are shifting away from commodity grade OSB, emphasizing
instead new and innovative products. LP is converting its Hayward plant to ¡®SmartSide¡¯, and its Houlton plant to
Oriented Strand Lumber (OSL). At the same time, the company is adding more capacity for
its ¡®TechShield¡¯ radiant barrier sheathing. This product features a thin
durable sheet of aluminum overlay laminated to OSB. It is already made at six of LP¡¯s locations in Georgia, Texas,
and British Columbia, Canada. Norbord increased its share of specialty products from 20% in 2006
to 25% in 2007. Their main specialty products are Solarboard, Tall Wall, Windstorm, and
Stabledge. Martco is also shifting its emphasis towards value-added products.
|